Overview: M.S. Research
M.S. Advisor: Professor Ulrike G.K. Wegst | April 2015 - August 2016
For my M.S. research, I designed, built, and tested new, multipurpose freeze casting equipment to address the current limitations in freeze casting with two main aims:
Aim 1: Enable experiments that increase the fundamental understanding of the freeze casting process.
Aim 2: Improve the manufacturing process by creating equipment capable of fabricating larger samples in new shapes.
My overarching research approach was to iterate efficiently while keeping designs and experiments simple and cost effective. The goal was to identify and tackle as many problems as possible and prototype solutions that would guide future work.
Background: Freeze Casting Process
Freeze Casting is a material processing technique that utilizes directional solidification and phase separation in solutions or slurries to fabricate microporous structures with highly aligned porosity. The process consists of three main steps: solution/slurry preparation, unidirectional solidification with a thermal gradient (freezing), and lastly sublimation of solvent.
The image shows the typical microstructure of a sodium alginate freeze cast material. The polymer solution was unidirectionally solidified and then the ice was sublimated away, leaving the resulting structure.
Schematic of a typical single side freeze caster and freezing process. The slurry is poured into a PTFE mold with polished copper bottom. PID controlled resistive heaters control temperature. The copper rod is immersed in liquid nitrogen and acts as a heat sink. (b) Controlled freezing results in the formation of lamellar ice crystals that expel the particles and/or solutes and are concentrated in the space between the crystals. (c) The crystals template the structure and after sublimation the resulting structure is highly-aligned and porous, as the SEM images show. Reproduced from U. G. K. Wegst, H. Bai, E. Saiz, A. P. Tomsia, and R. O. Ritchie, "Bioinspired structural materials," Nat Mater, vol. 14, pp. 23-36, 01//print 2015.
Horizontal Freezing Stage
The horizontal freezing stage (HFS) was designed to facilitate experiments to study the kinetics of ice-phase growth and mechanisms of ice templating in ice-polymer composites. In-situ light microscopy of controlled directional solidification would be the basis of such experiments. The primary goals were to:
- Observe the formation and progression of Mullins-Sekerka instabilities that cause the primary dendrites to form as a function of polymer concentration and cooling rates over long relative distances (~50 mm).
- Study conditions to enable single domain growth using microfluidic channels and Hele-Shaw cells.
- Create planar, cellular, and dendritic solidification fronts to observe, under controlled conditions, the microstructure interactions of the growing ice crystals.
Theses primary goals required a new solidification stage to be designed. The need for a new stage created an opportunity to pursue new and improved capabilities for fabricating freeze cast materials. By designing a multipurpose device, secondary goals could be pursued such as:
- Demonstrate a modular cold block design that could allow for multiple cold blocks to be configured in a flexible manner for emerging needs and experiments.
- Fabricate larger samples in new shapes, specifically sheet materials.
- Double sided freezing capabilities.
Rational
Optical microscopy is a simple, yet powerful experimental technique
Required to produce planar, cellular, and dendritic freezing fronts
Frosting can obscure the solidification front
Samples are solidified by immersion: speed control required
Sheet materials require larger surface areas
Reduces cost
Design Specifications
Capable of in situ optical microscopy of solidification
Precise temperature control
Mitigate frosting
Positioning control
Large surface area for freezing and able to accommodate freeze cast molds
Adapt existing materials and equipment available in lab
Achieved Value
- Less than -60 ̊C.
- Approximately -3.5 ̊C/min
- Pass: GUI allows user to set ramp / soak rate or stabilization set point
- Tested to 10 um/s
Design Requirements
Temperature Range: 60 ̊C to less than -40 ̊C
Cooling Rate – for sheet materials: at least -2 ̊C/min
Temperature control: ramp / soak and stabilization
Immersion speed: less than or equal to 15 um/s
Design

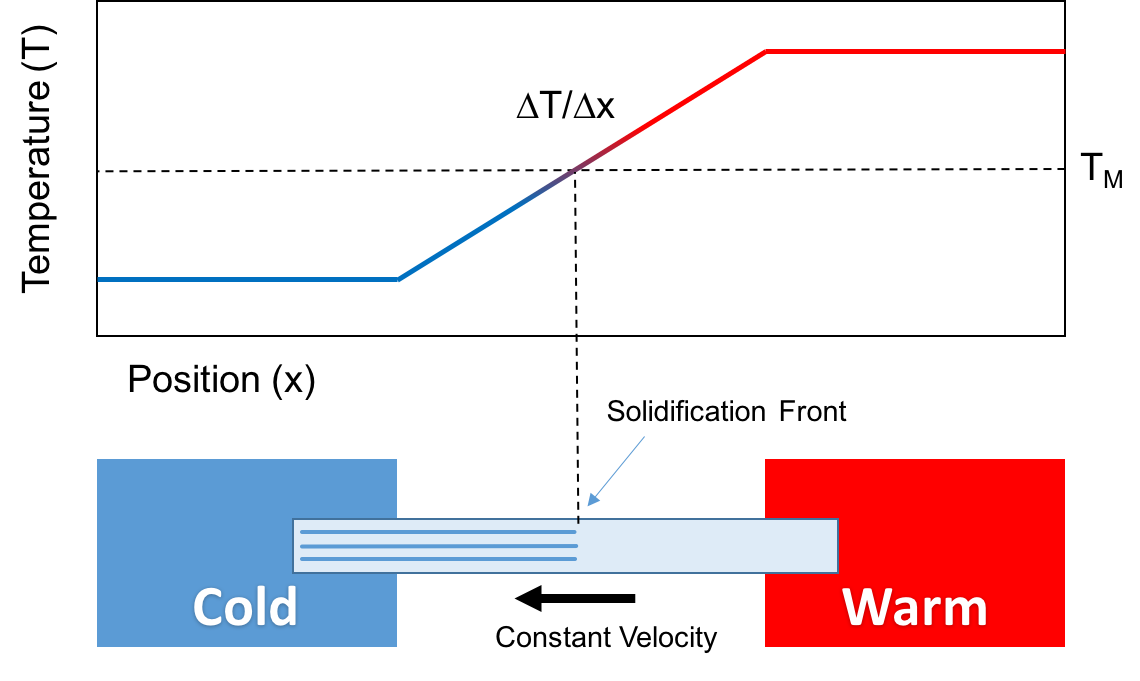
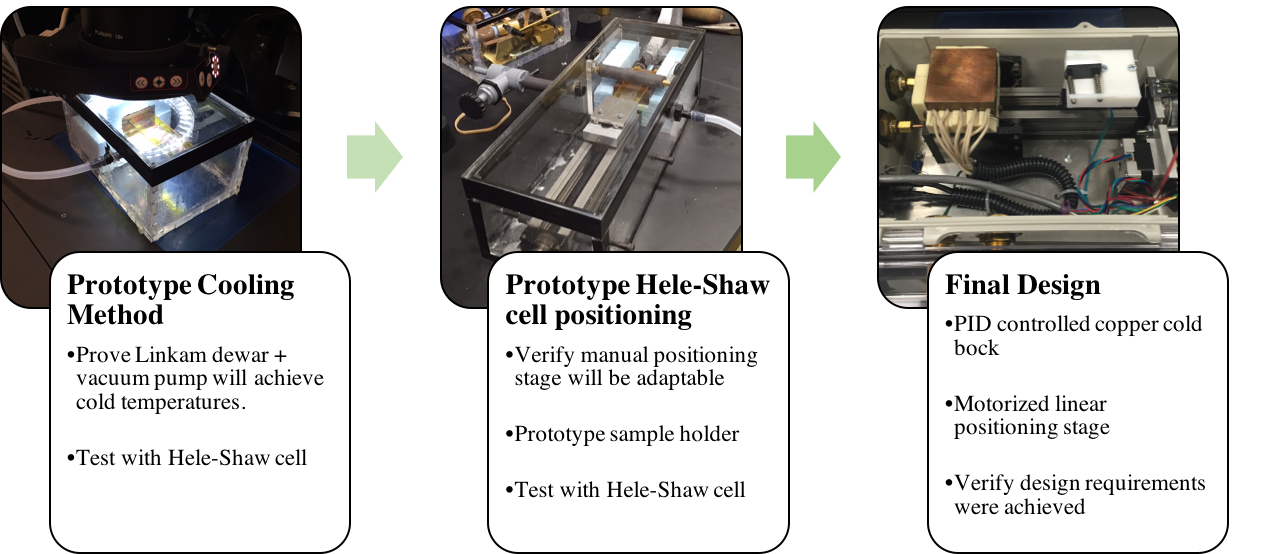
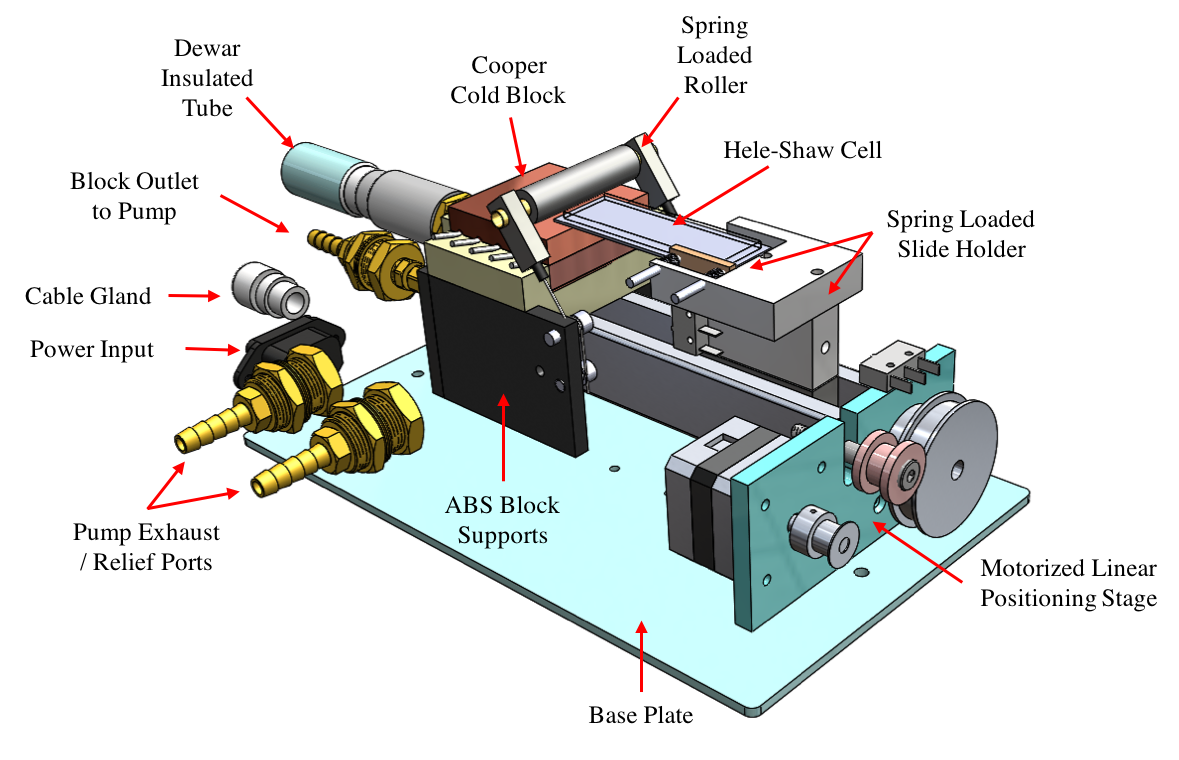
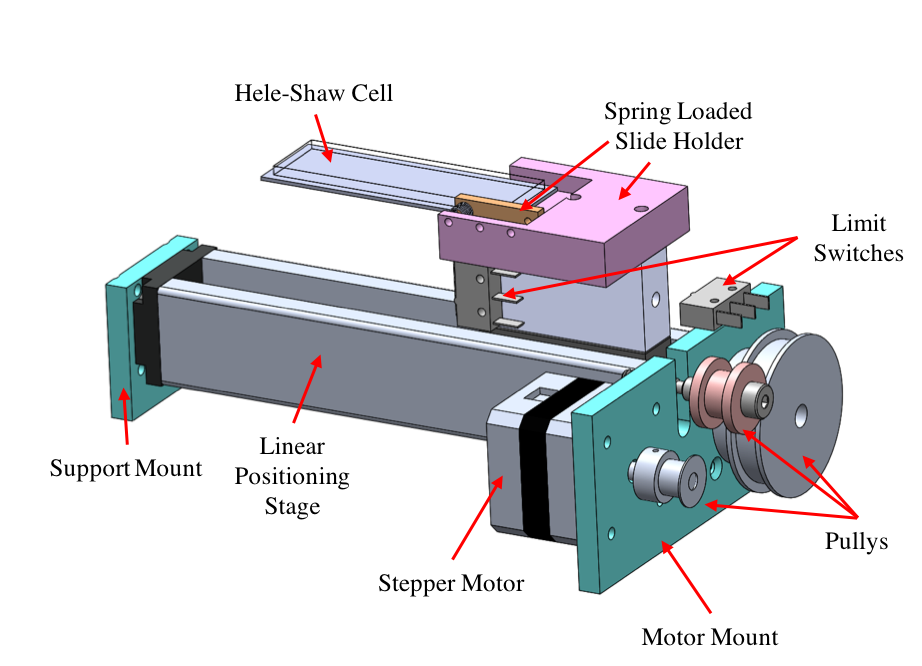
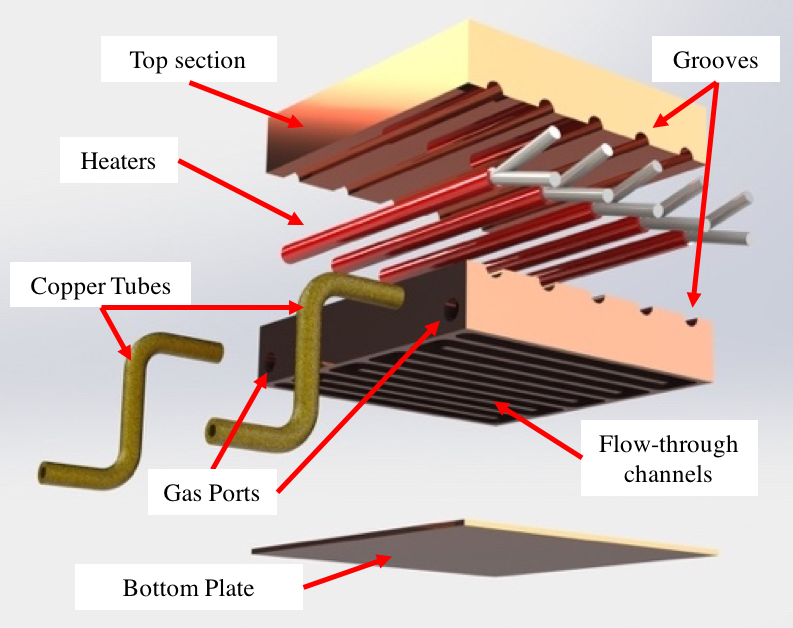
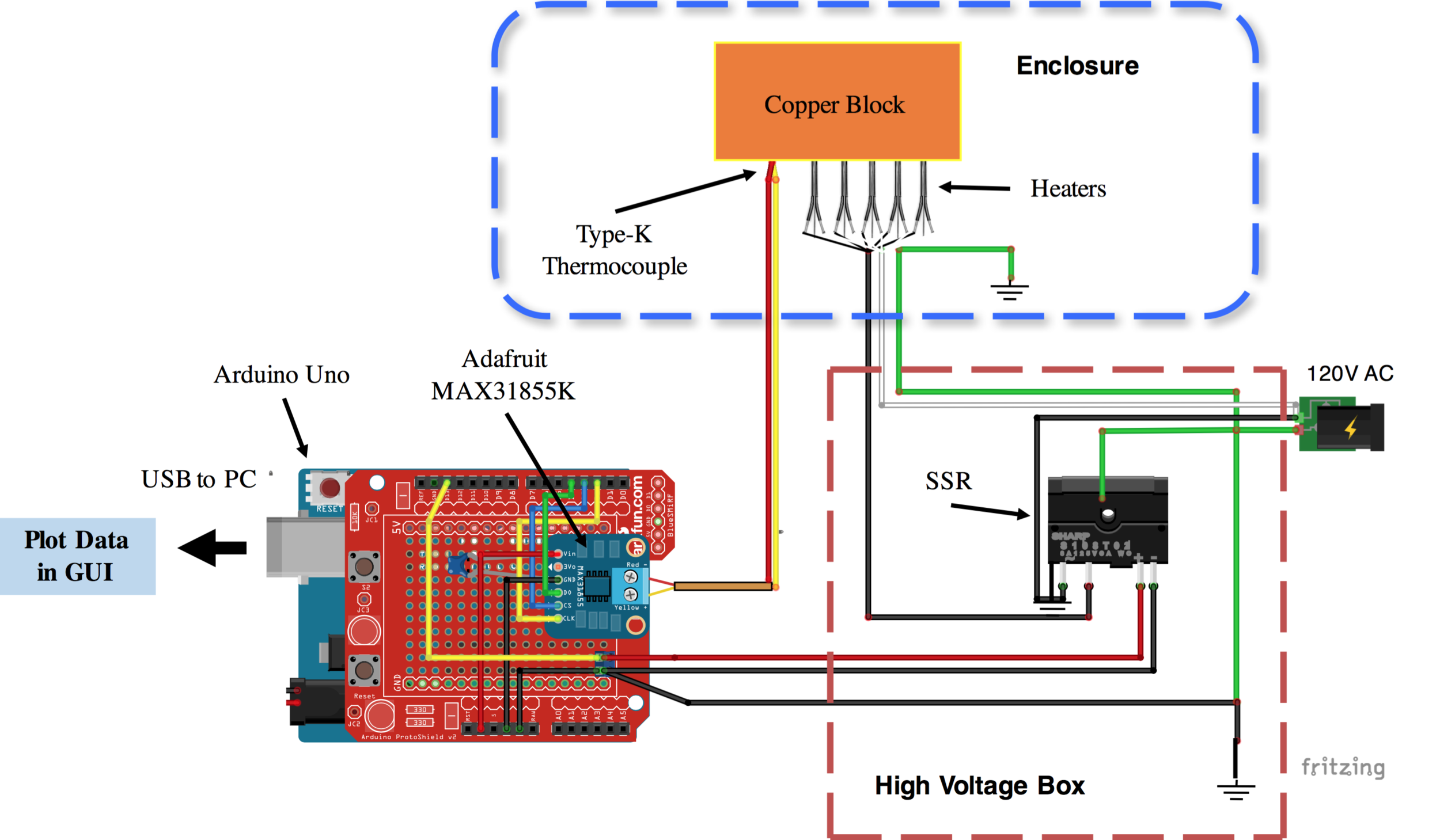
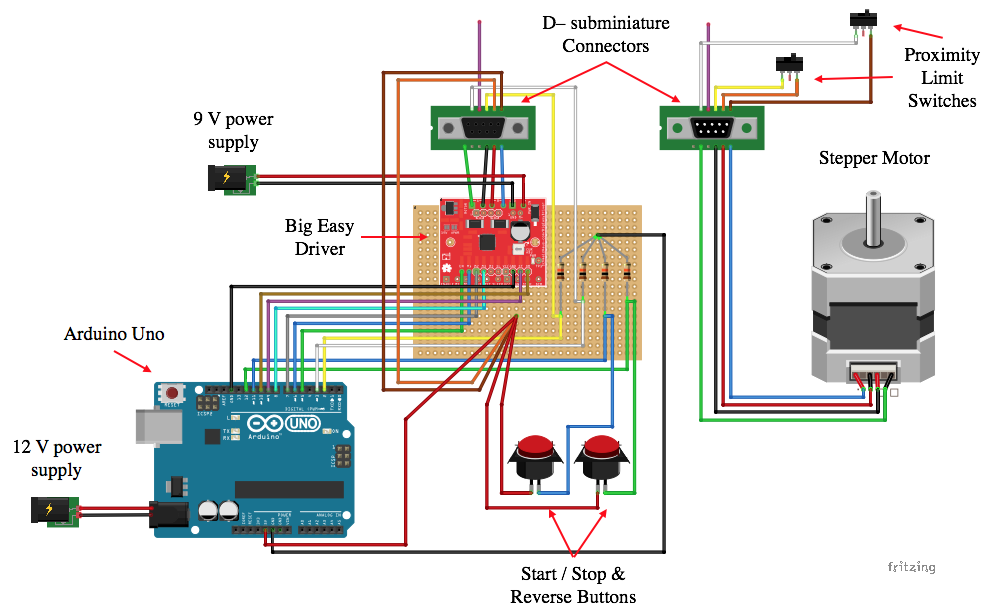
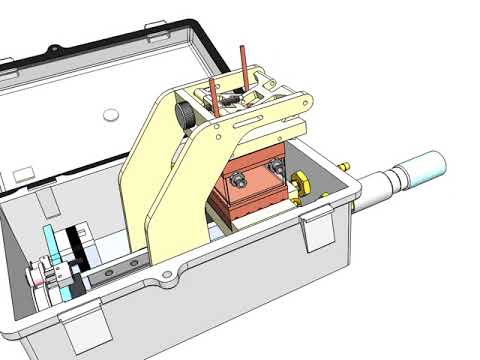
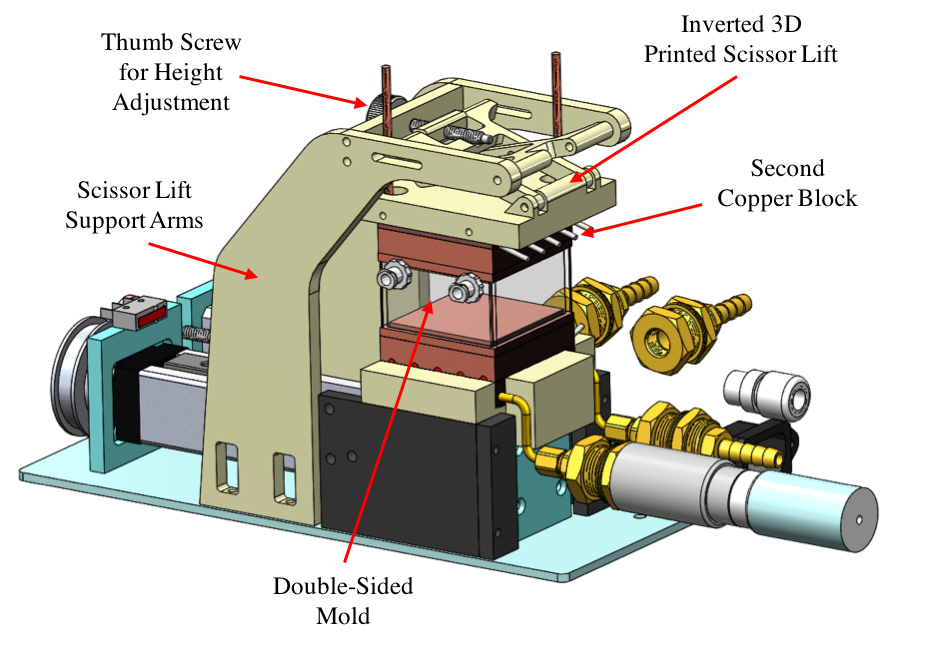
Build
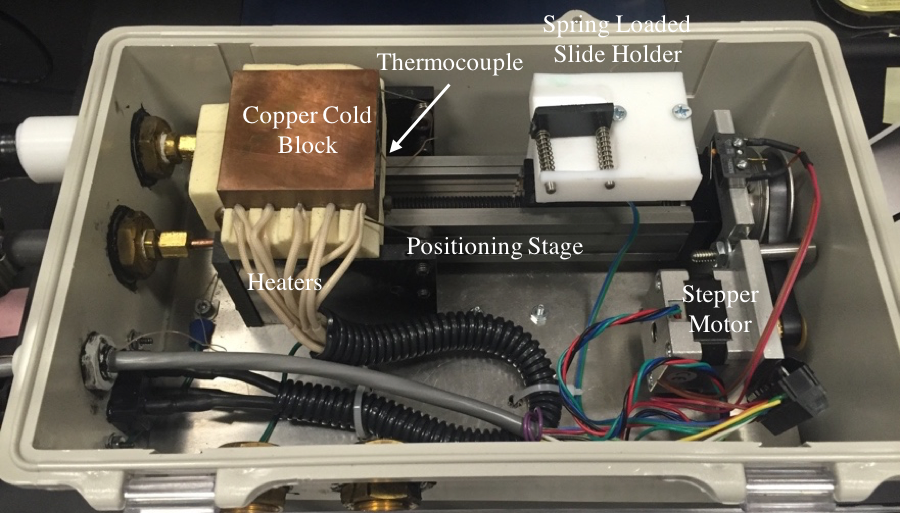
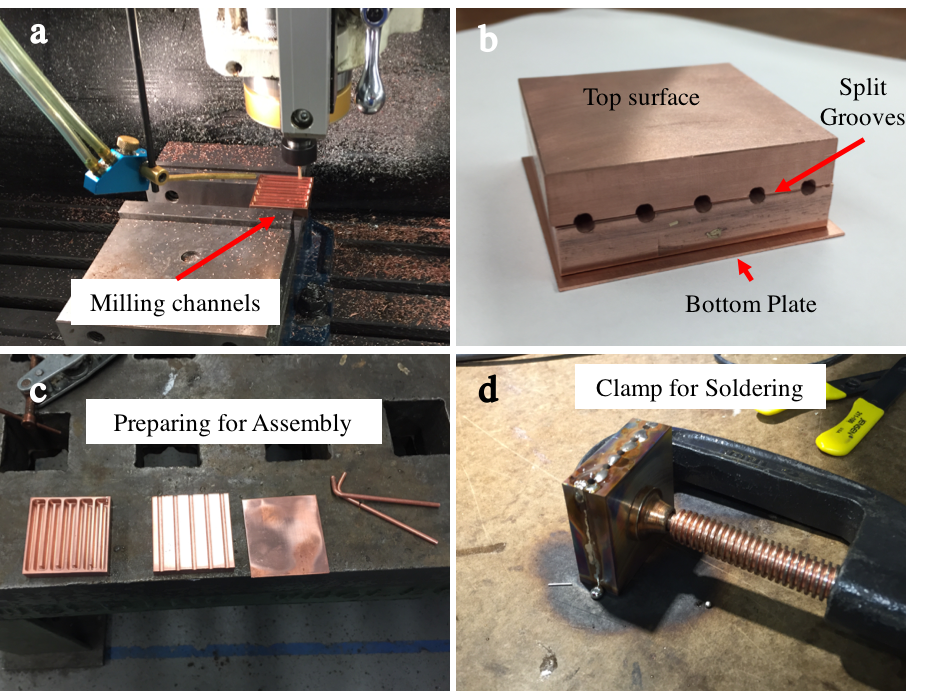
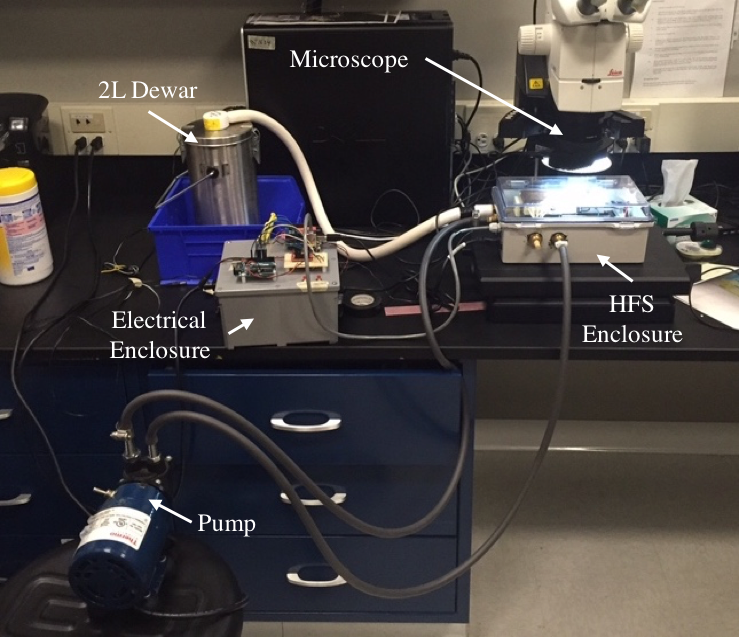
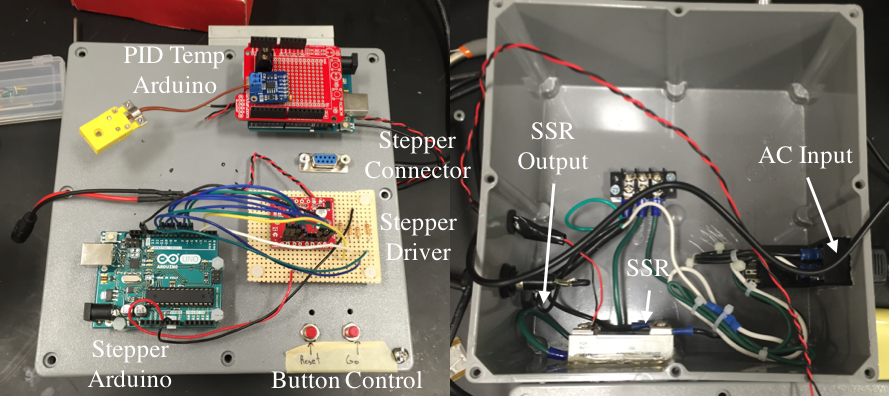
Test
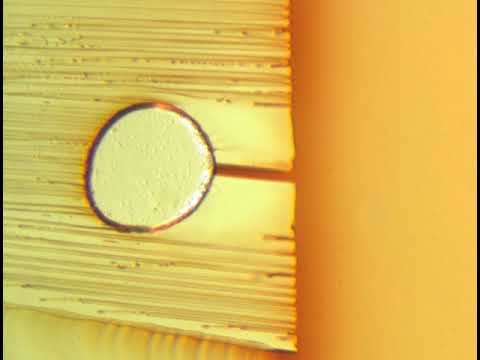
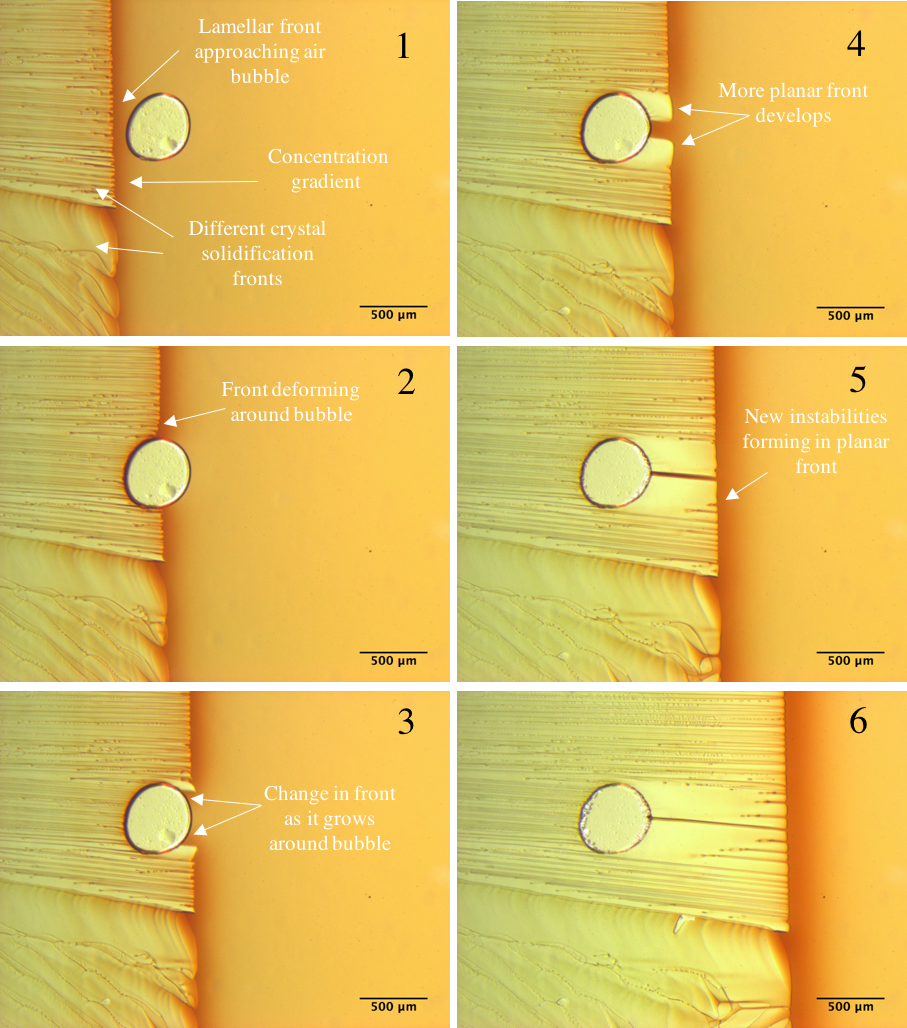
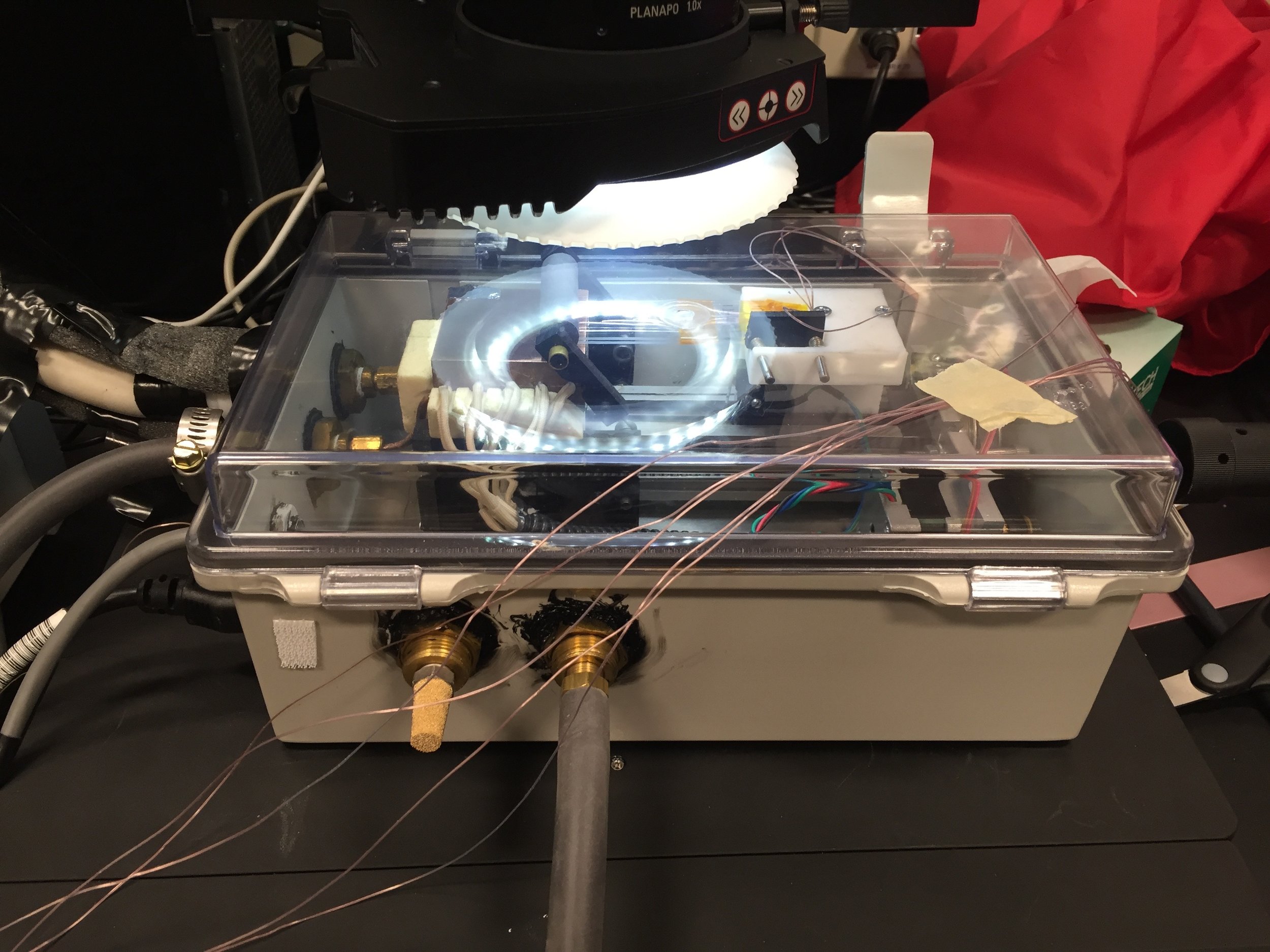
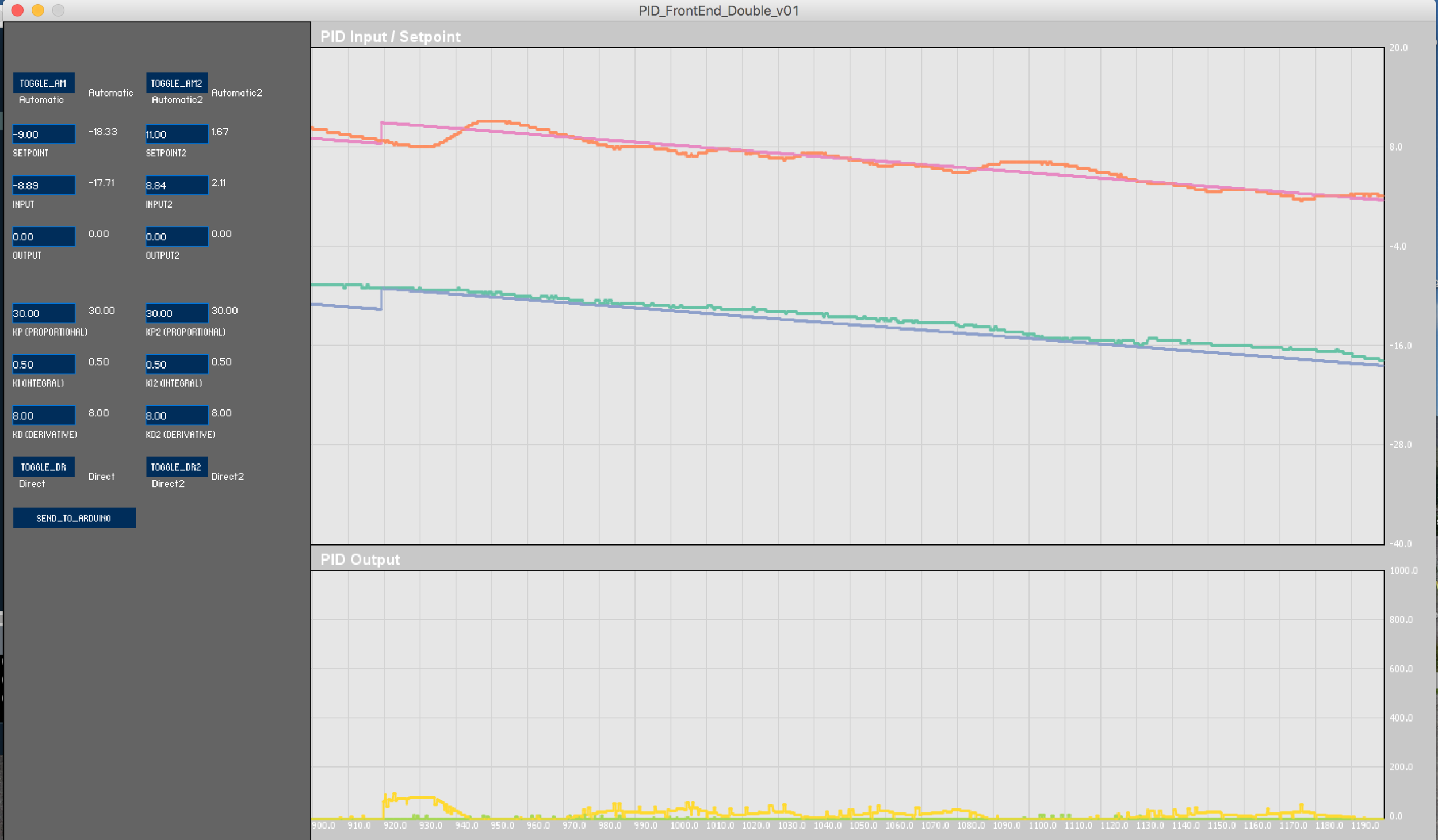
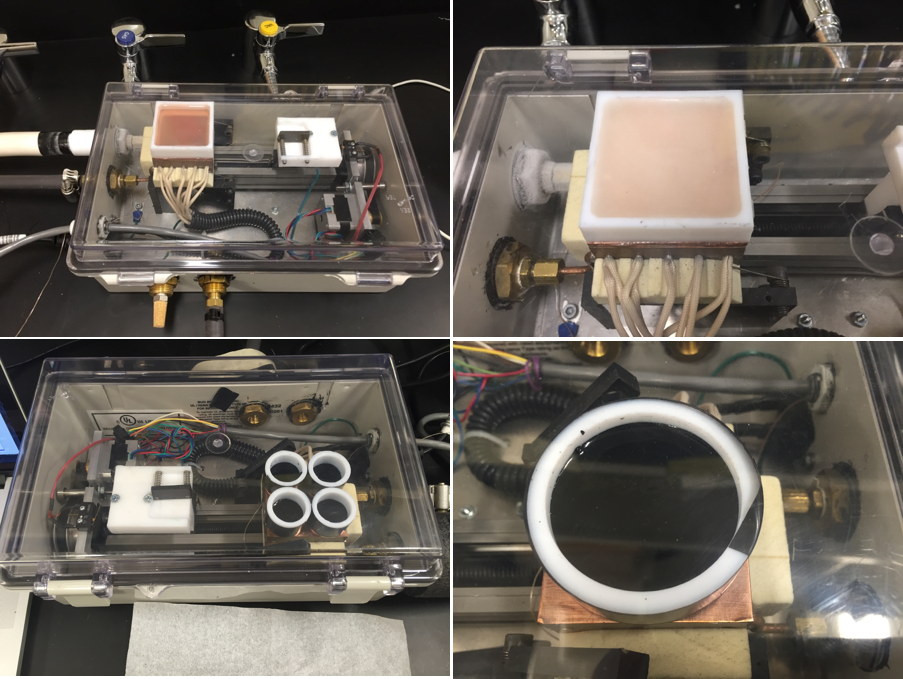